The idea of a “line of light” is not a new one. Linear lighting effects are among the most effective at rendering architectural and interior shapes and forms. Often, the light source itself is concealed, and only the effect of the light on nearby surfaces is seen, such as with cove lighting, niche lighting and undershelf lighting. Lines of light can be used to edge-light glass and acrylic panels. More recently, lines of exposed luminaires are used to create interconnecting lines of light across ceilings and walls. Linear designs are also becoming popular for exterior lighting.
This is especially significant because legacy light sources limited line of light options. Incandescent festoon lamp strips are too hot, neon lamps require custom lamps and high voltage, and fluorescent lamps are big and clumsy. And there was always a lot of cost involved. Before the LED era, line-oflight designs were impractical and uncommon.
Among the most practical and unique abilities of LEDs is that low wattage LED sources can be mounted to a flexible tape. Tape light is very compact – the tape and a simple extrusion can be as small as ¾” wide and 3/8” tall and can be surface mounted or routed into building elements like a ceiling, wall or the bottom of a shelf or a cabinet. With a wide selection of colors of white, monochromatic, white light tuning or RGB color, the range of achievable effects is quite broad. Even high CRI products are moderately priced and readily available. It is low voltage and dimmable and can operate from plug-in power supplies as well as hardwired power supplies. There are even special versions of tape light designed to be used in wet environments, with the LED’s and tape sealed in a clear watertight compound including a version capable of being completely submerged. Best of all, tape light can be inexpensive and for DIY installations, can be purchased from online stores or lighting showrooms with all the parts you need to actually do-it-yourself.
Tape light is literally a tape onto which are mounted low wattage LED’s. The tape is a heat-conductive, thin and flexible insulator with circuit-board traces on the side opposite the LEDs. Connect a DC power source to one end, and the LED’s emit hemispherical diffuse light. It is sold in reels with adhesive insulation on the back side that permit the tape to be stuck directly onto an aluminum extrusion that mounts the light to a surface and acts as a heat sink for the LED’s.
Depending on the number of LED’s per foot and their wattage, a tape light can generate up to about 800 lumens per foot (2,600 lumens per meter), although I suspect that most applications are between 100 and 400 lumens per foot. Considering that this light is emitted only to one side, it is much more effective than conventional fluorescent lamps but a fraction of the size. Tape light systems can provide general illumination, task lighting, ambient lighting, wallwashing, and a number of special effects that are impractical and nearly impossible with other light sources. For instance, in the design of restaurants, lighting the knee space under the customer’s side of a bar serves to light the floor and causes the bar top to seem to float, while not affecting the customer’s view once seated. Once impractical, it is almost standard practice today with tape light.

Courtesy of Q-tran
“Before the LED era, line-of-light designs were impractical and uncommon.”
From an electrical point of view, most tape light is called “constant voltage”, which means a steady DC power source feeds one end and all LED’s operate together. In the US, most tape light is either 12 volts or 24 volts DC. Tape can be field cut at regular points, generally every 4 to 12 inches marked on the tape. Because tape is low voltage, inexpensive power supplies and low voltage control components can be used for everyday applications like lighting inside of cabinets and drawers using magnetic reed switches or tiny PIR motion sensors.
Dimming is a little tricky, however. Because tape is usually constant voltage, regular phase-cut dimming will result in significant 120 hertz flicker except at full light. To minimize flicker, use of pulse-width modulation (PWM) dimmers operating at 400 hertz or more is recommended. This complicates installations a bit, but with 0-10-volt dimmers and a PWM dimming module or power supply, flicker free results are readily achieved. For bargain installations and to save cost , a low voltage manual PWM dimmer can be installed at the end of the tape, especially if there is an on-off switch in an appropriate location and the dimmer is infrequently adjusted.
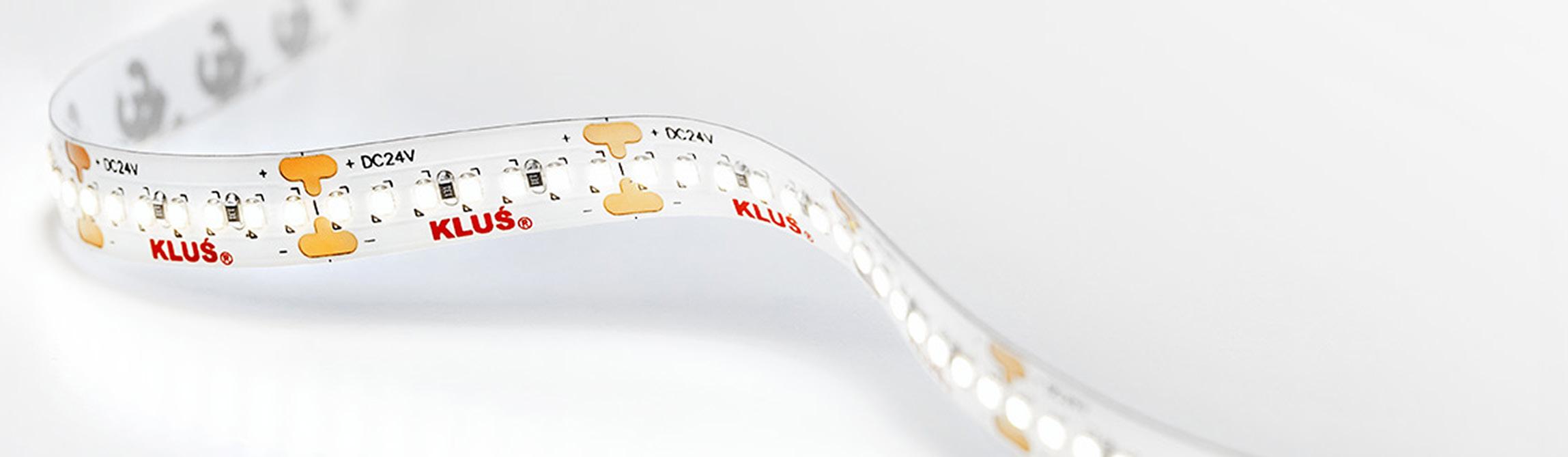
Courtesy of KLUS
To the design and construction professional using tape light, I recommend the following additional considerations: Get some tape light and test it. Its easy and safe to work with, and it will allow you to understand how much light you need. You will learn firsthand the necessary light output for various applications.
Explore the dozens of different extrusion types. There are angled extrusions for wallwashing, mud-in extrusions to create lines in ceilings and walls, shallow and deep extrusions for various applications, and special extrusions and fittings for corners and ends.
A diffusing lens should be used when a reflection of the light sources may occur. This is especially true for undercabinet lighting when the counter below is polished stone.
A new generation of sophisticated optics is entering the marketplace. Some will enable asymmetric linear effects such as asymmetric cove lighting and gradient wallwashing, very worthwhile to the lighting design professional.
Outdoors, consider a sealed linear lighting product with a lens. While waterproof outdoor-rated tape light will work, it will be difficult to keep clean and will accumulate dirt.
Finally, thoroughly study the candidate manufacturers and their products. For the best and most professional outcomes, I strongly recommend made-to-order tape light. The contractor measures the planned installation and sends the information to the manufacturer, who then makes each piece and ships it very quickly. Cutting and making up field connections in the field with tape light is difficult and often results in intermittent or faulty connections. Factory made connections ensure long term performance without sections of tape going dark. I’ve been working with tape light for over 10 years, including in my own home and office, and I’ve learned the hard way about bad connections. In the end it is not more expensive compared to electrician’s work and the result will be better.
This article originally appeared in the December 2020 issue of designing lighting.