Energy-saving goals and energy codes require more functionality and flexibility from today’s lighting control systems over the lighting controls that were on the market 20 years ago. Modern lighting control systems are more secure and offer more flexibility and scalability for a single room to an entire campus of buildings. Advanced lighting control systems allow the design of a space to focus more on the effect of lighting on its occupants.
With increased functionality comes more perceived complexity related to installation and commissioning. Manufacturers have introduced solutions employing plug-and-play technology, simplified wiring, apps for configuration, and other technologies to make the installation and commissioning process easier. However, even with these features, installation and commissioning may still seem complex and not as intuitive, especially if the installer is unfamiliar with lighting controls.
The good news is that several steps can be taken to prepare for a successful installation and commissioning process, with each step involving ongoing communication and collaboration between all parties involved.
- Setting the stage for success with the Owner’s Project Requirements (OPR)
- Specifying quality control with the Basis of Design (BOD)
- Ensuring occupant satisfaction with end user training
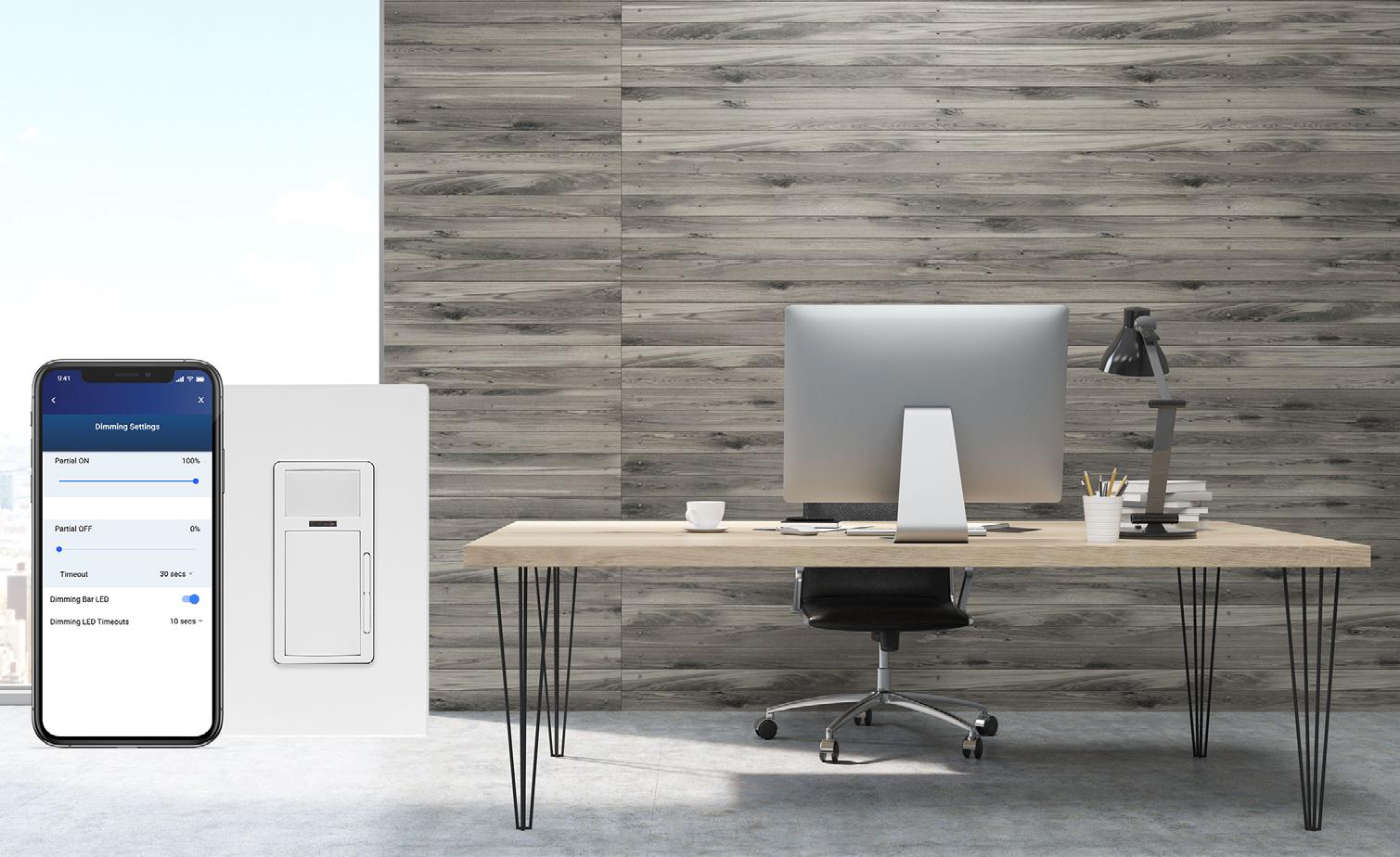
Defining Commissioning
Some customers may be unfamiliar with the different technologies and their limitations as well as energy code requirements, so creating a comprehensive OPR can be an investment in time, but it’s an investment well spent. The time with the customer sets the stage for selecting the right product for the right application and allows the system to be configured to meet the customer’s intent. This discovery and planning phase can also help eliminate unwelcome surprises in the following steps and at installation and commissioning.
Commissioning is the process of activating lighting control systems so the installed equipment performs as intended and meets the design intent and owner requirements. Simply put, it’s the process of ensuring that the lighting control system provides the right amount of light where and when needed.
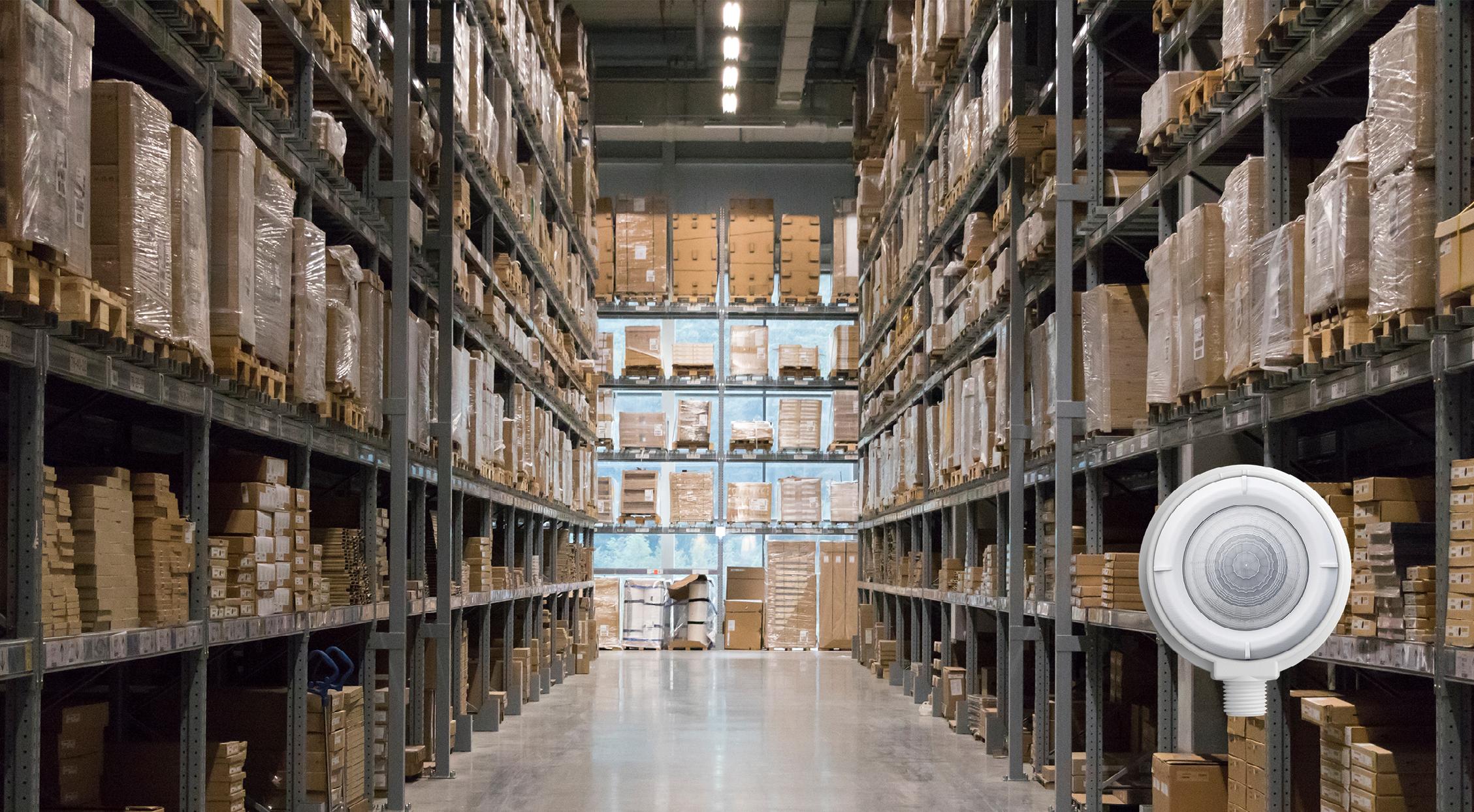
Setting the Stage for Success with the Owner’s Project Requirements (OPR)
Part of the pre-design and pre-site visit should include identifying and understanding the customer’s project requirements and establishing project objectives. How will the facility be used and how should the lighting control system perform? What do they want and need the lighting control system to do? All these details should be documented in an Owner’s Project Requirements (OPR) statement to ensure all parties have clear expectations for the project and used as a reference throughout the entire design and construction process.
Details should include requirements for individual spaces and how the lighting should operate in those different spaces. Elements should include a description of the various tasks the space will be used for as well as unique architectural considerations that may impact the lighting. Lighting considerations should also include aesthetics, light levels, color, and visual comfort preferences. During this process, zones, energy-saving goals, and the need to meet energy codes and standards should also be identified as well as maintenance and technology requirements.
Multiple elements will determine the selection of the lighting control components, the technologies to use, the functionality and complexity of the lighting control system that will be installed, as well as fixtures. Elements includes project budgets, required lighting levels, controllability, space usage, efficiency goals, and maintenance requirements.
Specifying Quality Control with the Basis of Design (BOD)
The Owner’s Project Requirements (OPR) help create the Basis of Design (BOD) and give all parties a plan on how to proceed in the right direction. The BOD should clearly describe the lighting control system and a well written Sequence of Operation (SOO) that precisely details how the lighting controls should operate in each space in response to different situations. The SOO should describe the requirements for all the different space types, including specific criteria for device settings, light levels, switching, dimming, dimming levels, timeouts, daylight harvesting, scheduling, scenes, demand response, and more.
Similar spaces in the same facility can have different control requirements. It can range from spaces requiring multi-zone dimming and daylight harvesting to varying light level preferences for occupants in the same zone. This critical document should be referred to throughout the design and construction process with any changes clearly communicated, documented, and agreed to by all parties. Having these details in advance provides the information that the commissioning team needs to ensure that each space is working as intended.
Additional consideration should be given to the installer and ensuring that they are familiar with the product being installed with the manufacturer providing training if needed. Documentation should include drawings that provide all equipment details, wiring connections, mounting details, and other relevant installation information. Limitations for the products should be included as well to ensure no assumptions are made and the installation is optimal. All this information can be extremely helpful in addressing and preventing common issues that can arise on site.

Ensuring Occupant Satisfaction with End User Training
Successfully completing the Owner’s Project Requirements and Basis of Design will ensure a smoother installation and commissioning process. Once these steps are completed, the owner or facility manager who will be responsible for operations and maintenance should be trained on how to correctly operate, maintain, and modify the lighting control system.
One additional item that gets overlooked is the importance of educating occupants on how the lighting controls should operate. Being unfamiliar with the features and functions of the new system may cause them to presume it is not functioning properly. It might be as simple as not knowing that an occupancy sensor was installed with a pre-determined timeout that was programmed for the space or a schedule that was implemented for the lights to dim up and down or on and off during certain times of the day or as simple as operating keypads with pre-programmed scene controls.
Training occupants will help them understand why the new control system has been installed, how to operate it, and what to expect. Educating occupants on how the lighting controls will perform after a retrofit or move-in can be highly effective in contributing to occupant satisfaction and avoid having them try to override or bypass the system.
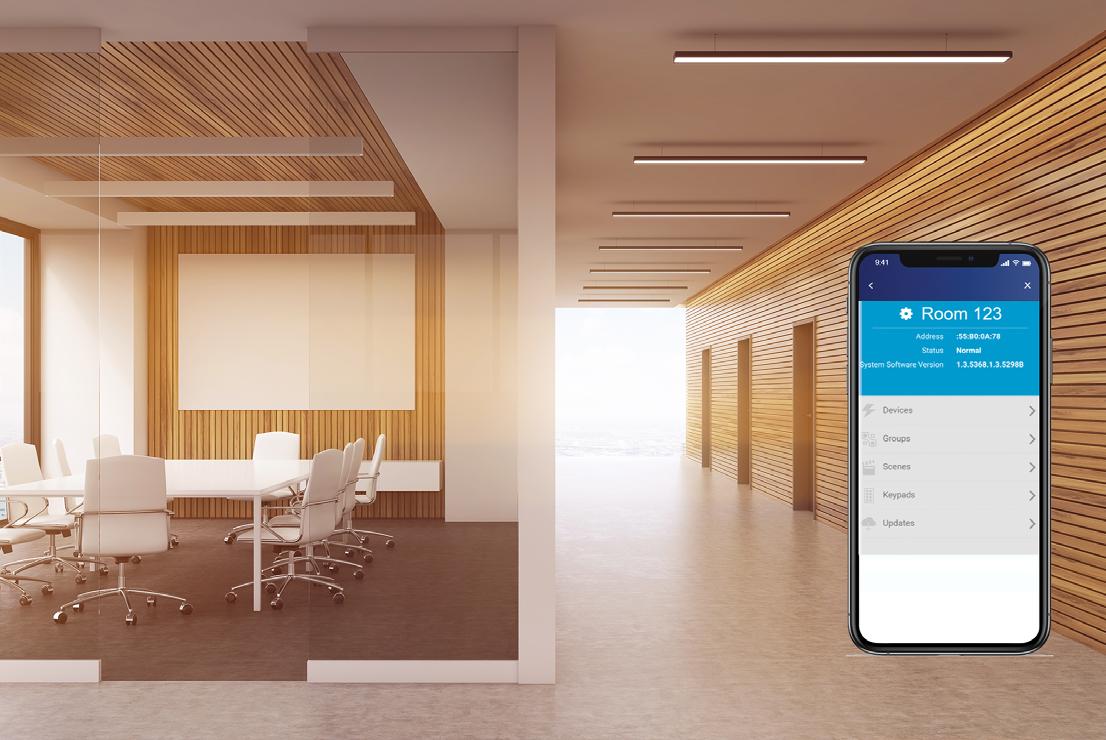
Partner with the Right Manufacturer
Promote a smoother installation and commissioning process for lighting control systems. It all starts with a comprehensive understanding of your customer’s needs and requirements to install a lighting control system for optimal performance, occupant preferences, and energy savings. The key to success is communication between all the parties involved.
The whole process should be a collaborative one where the customer partners with the right design team and manufacturer who will ensure top-notch service and support every step of the way from product selection and design to project delivery and customer handoff.
This article was originally featured in the October issue of designing lighting (dl).